Let’s face it: empty automation positions in manufacturing aren’t just a nuisance; they can seriously hurt your bottom line. I can’t tell you how many times this topic has popped up in my conversations with manufacturing leaders. It’s bigger than it looks, and the impact can really sneak up on you.
First, let’s talk productivity. I recently worked with a food processing plant that had an automation engineer role sitting open for six whole months. You can guess what happened—upgrades were put on hold, existing systems were underutilized, and they estimated a whopping 15% hit to their efficiency. That’s a significant loss, and it piles up quickly.
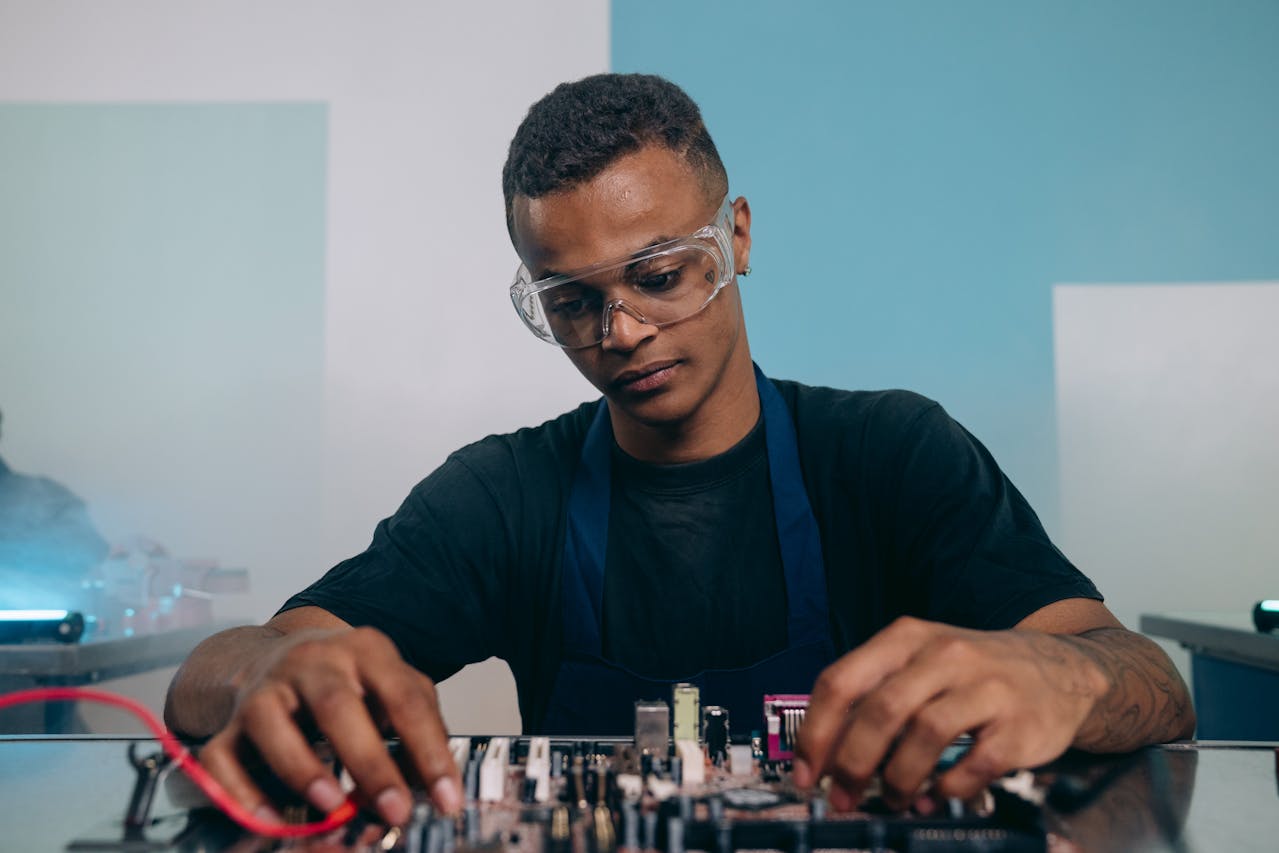
But the fallout doesn’t stop there. Unfilled roles also create tension within your existing team. I’ve seen burnout creep in because employees are stretched too thin, trying to pick up the slack. In fact, one of my clients lost two crucial team members because they couldn’t handle the extra pressure. The cost of losing experienced staff? Trust me, it’s way more than the expense of hiring in the first place.
Then there’s the innovation piece. Automation is like a fast-moving train—it doesn’t sit still. If you’re short-staffed, you’re just trying to keep up, not pushing the envelope or exploring new technologies that could really set you apart from the competition. I’ve watched companies fall behind because they couldn’t keep up with advancements due to understaffing.
Quality is another major concern. When your automation systems aren’t well-maintained or optimized, mistakes start to creep in. One manufacturer I worked with noticed a spike in customer returns that traced directly back to their understaffed automation team. The cost of lost business and a tarnished reputation can be brutal.
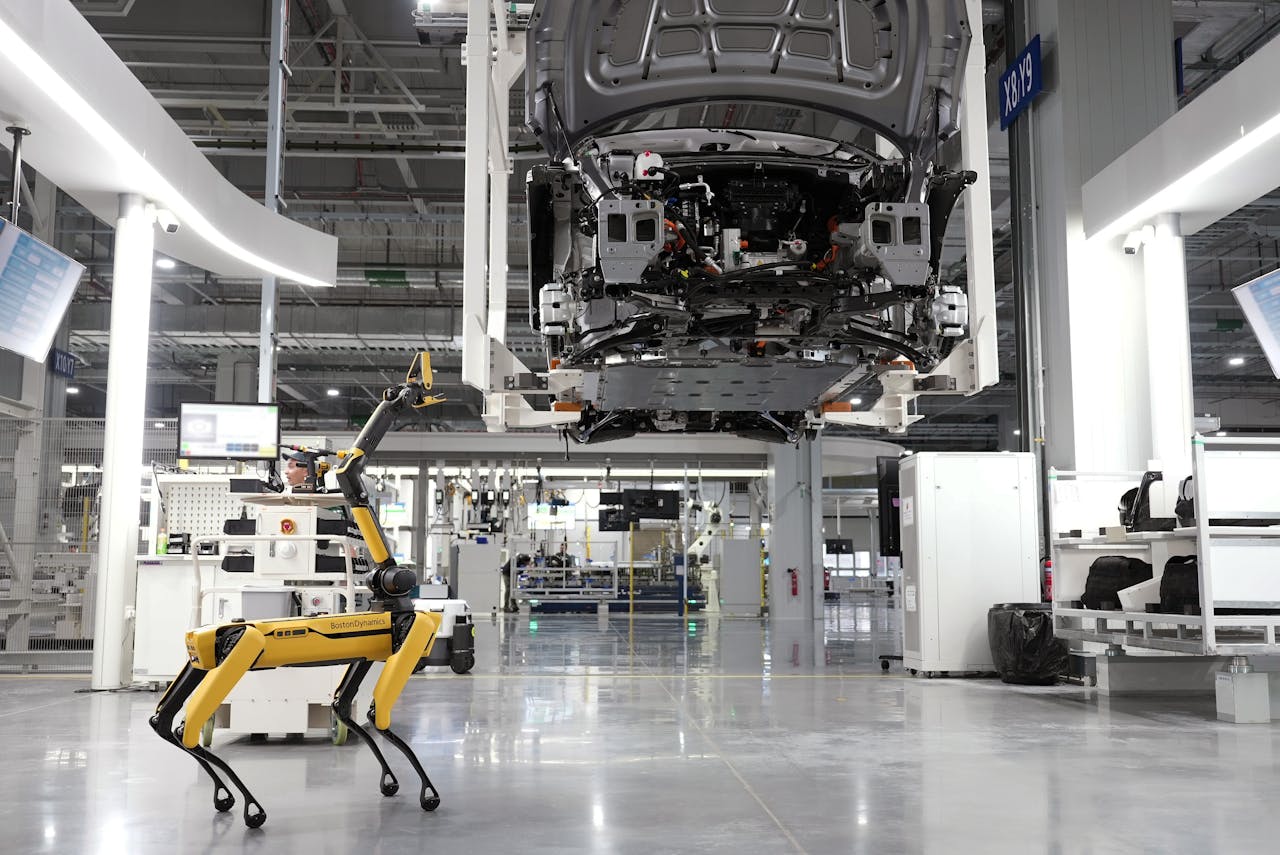
And let’s not forget the snowball effect. The longer a position stays vacant, the more pressure it puts on your team, which can lead to even more turnover. It’s a cycle I’ve seen too often, and it’s never pretty.
So, what can you do? First off, be proactive with your hiring. Don’t wait until you’re in a bind to start searching. Also, consider bringing in interim solutions like automation consultants or contractors to help you keep the wheels turning while you find the right fit. And remember, investing in retention is crucial. It’s almost always cheaper to keep your good employees than to lose them and start from scratch.
In a nutshell, those unfilled automation positions are costing you more than you might realize. It’s not just about the salary you’re not paying—it’s about lost productivity, missed opportunities, and quality issues that could come back to bite you. If you’re ready to dig into the real costs of those open roles, let’s chat about some strategies to turn things around.