Let’s be real—the manufacturing world is buzzing with automation, and it’s changing the game faster than ever. But here’s the catch: this shift isn’t about robots taking over jobs; it’s about getting our workforce ready to work alongside these new technologies. I’ve seen some exciting approaches that manufacturers are taking to tackle this challenge.
Start with the Right Mindset
First up, mindset is everything. I’ve seen some fantastic results when companies start by being open and honest about what automation means for their teams. One large auto parts manufacturer I worked with held a big company-wide meeting to kick things off. They laid out their plans, addressed any worries, and, most importantly, emphasized that this was a chance for growth rather than a threat to jobs. This transparent approach helped reduce resistance and sparked enthusiasm among employees to learn new skills.
Empower Your Team with Training
Next, let’s talk about training. I love the “train the trainer” method. At a food processing plant I worked with, they identified their most tech-savvy line workers and sent them off for specialized training on the new automated systems. When these workers returned, they became internal experts, teaching their peers and acting as a link between the automation team and the shop floor. This not only fostered a sense of pride but also helped everyone feel more comfortable with the changes.
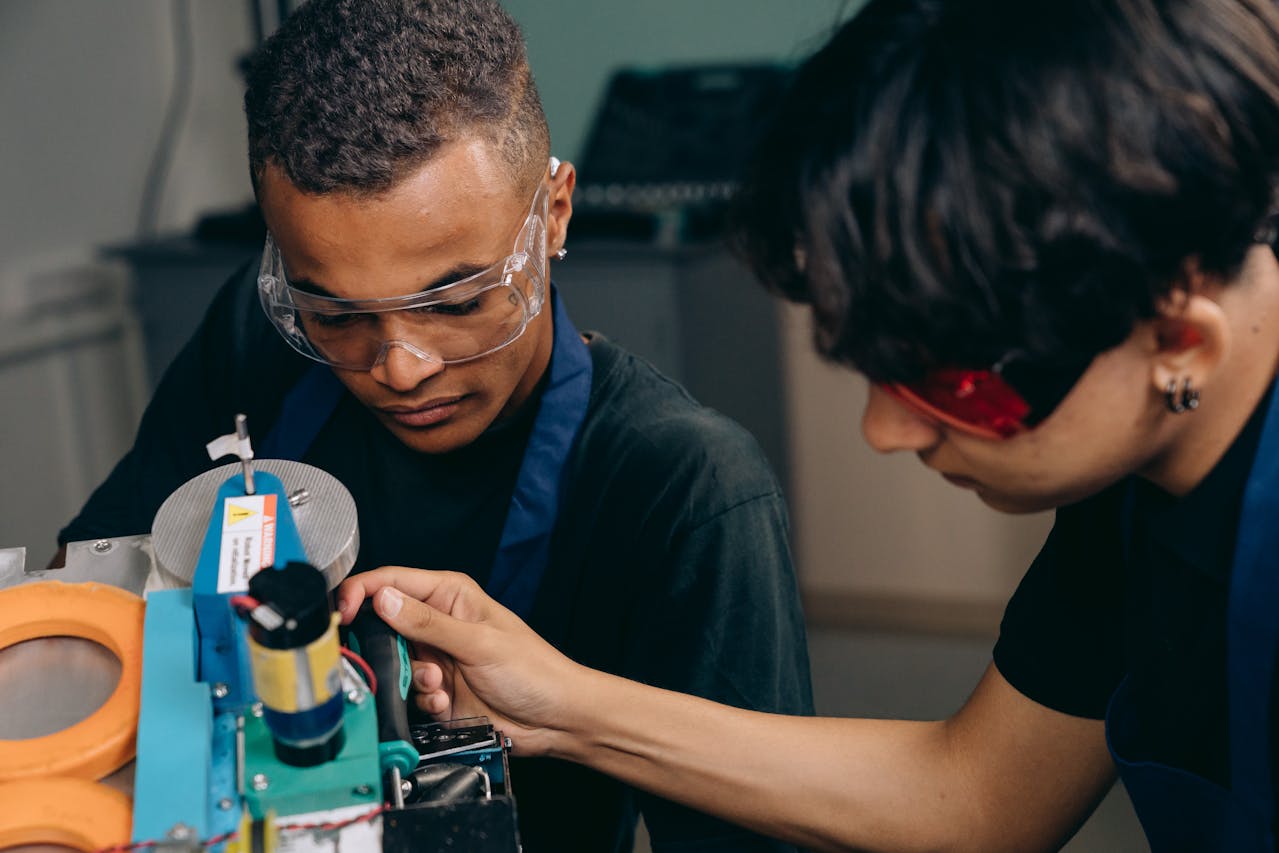
Hands-On Learning Is Key
Hands-on experience is crucial, too. Sure, classroom training has its place, but nothing beats getting your hands dirty. One manufacturer set up a “sandbox” area where employees could tinker with new automated equipment during downtime. This not only took the pressure off but also encouraged creativity—people started coming up with ways to optimize processes just by experimenting.
Find Hidden Talent Within
You’d be surprised how many great automation pros began their careers on the assembly line. They understand both the technical side and the daily grind of manufacturing. So, don’t overlook your current team! That eager worker who’s always fiddling with machinery? They could be your next automation star.
Make Learning Continuous
And remember, reskilling isn’t a one-time event. The pace of change in automation means continuous learning is essential. Many companies are now using online platforms to offer flexible, on-demand training, keeping employees engaged and up to speed.

Don’t Overlook Soft Skills
Finally, let’s not forget about soft skills. As manufacturing becomes more automated, skills like communication, collaboration, and critical thinking are becoming even more important.
In the end, moving towards an automated environment is a journey. It takes time, investment, and a commitment to your people. When you get it right, you’ll have a workforce that not only adapts to new technologies but thrives in the process.
If you’re curious about strategies for reskilling your team or just want to chat about the future of manufacturing, I’d love to hear from you!